sus-PEN-ded - A History
The long walk to convenience. Follow our path of where the idea started and how the product evolved into what it is today.
How It All Began
Back in 2004 the director of Tundracode, Danie, was involved in a family business manufacturing paint and related products. In the retail store consisting of 2 sales counters and 1 tinting counter, finding the last used pen was just a nightmare. Box after box was vanishing as customers accidentally walked out with them or simply being misplaced to never surface again. As a result pens were quickly "borrowed" from the offices. Needless to say they never found their way back. Constantly looking for something to write with, pushed the frustration levels through the roof.
Comedy Relief
Here are just some of the frustrations turned into cartoons - to lighten the mood.
The one brother, Werner, just about had enough. He made a metal hook, screwed it in the ceiling, took some line, and had only one pen hanging with some wire nails acting as the counterweight running against one wall. Immediately the problem was solved. The only downfall to this was the fact that it wasn't a pretty sight and the line eventually left an ugly black mark against the ceiling and wall. Not long thereafter, the line would actually cut a groove into the metal, so deep, that the operation got very sticky and even cut the line. A little frustrating, but nothing compared to the previous scenario. That system was in operation until 2013 when a total revamp happened along with franchising options. The "unsightly" system was not allowed with the new professional look and since all the stores needed to conform to a certain look and feel , it was never put into operation again. Guess what?... pens once again "disappeared" like before.
Towards the end of 2014, Danie was inspired to make this thing work again. After a lot of thinking, a light suddenly went on presenting the idea of having two pens counterweighing one another. The first working model was made out of metal with machined rollers. sus-PEN-ded's first breath was taken as the system worked.
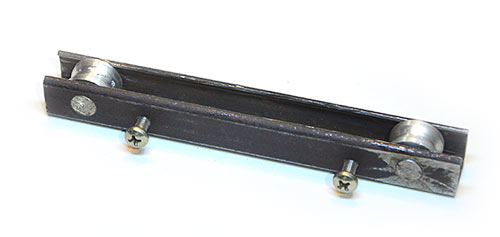
The first physical prototype - which mounted with another plate to the ceiling
January 2015 a patent search was done internationally. As there was nothing like it ever patented, and or sold publicly, the patent was filed for the concept of "Suspended Stationary". Danie then realized that it will consume a lot of time and effort to achieve the goal and left the family business in April 2015.
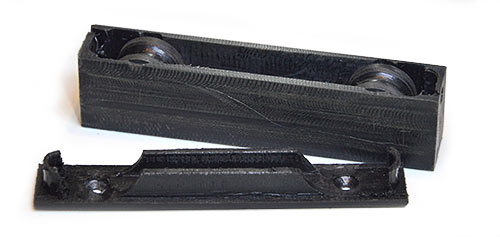
The actual unit that was submitted as a sample for the patent
Another prototype was made from plastic this time, also with plastic rollers. The rollers were a bit noisy during operation. Werner then suggested to use steel shafts instead. The operation was then quiet, but having the fear that the line will eventually cut a groove in the shaft again, hard chromed shafts were found to be the answer.
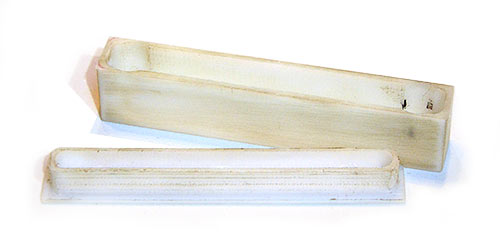
The unit that the tool and die makers used for the mould
When tool and die makers were approached, yet another to exact size prototype plastic unit was made, with solid shafts.
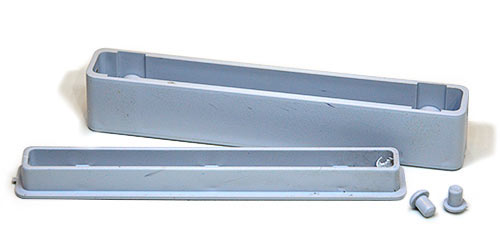
The first "final" sus-PEN-ded Holder to be produced
The very first unit from the injection mould manufacturers
Around October 2015 all the moulds were made and production was run on the first 2000.
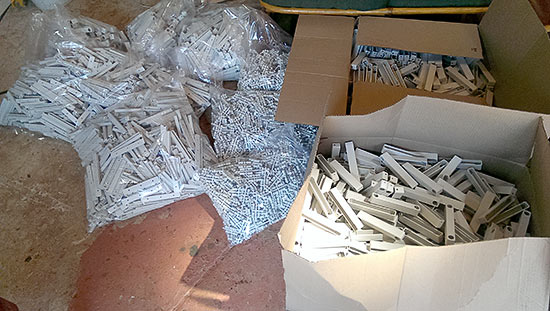
The first batch run of sus-PEN-ded Holders from where they went to the printers for branding
The final printed sample was then presented after some changes were made, but this unit has unfortunately been misplaced.
Offering enough fastening options to the customer for all the different types of surfaces out there was by far the most difficult part of the whole journey. Once the FIBERITE glue was chosen as the glue option, the container to pack and supply it in went from sachets to syringes to sealed drinking straws ... hours, days and weeks went into this before it was decided to make another mould and self-manufacture the small jars, airtight sealing lids and small spoons to scoop the product from the container.
Packaging and artwork was also not easy as there is no other product similar to this out there. No peeking or looking for ideas over the fence! During this time, having all the components but no packaging, people who were aware of the level of completion, just wanted stock to sell, or mostly to fit out their working stations. The family paint outfit was obviously first in line to have their problem solved. Then it happened, a unit was given for a friend who installed it right away. The next day the owner of the company walked into her office and wanted 10 units. Against will, selling incomplete stock, 10 units were sent out. Upon delivery another 10 units were ordered for their Cape Town branch and other offices!
After 5 months of waiting - towards the end of April 2016 - the packaging eventually arrived.